We have the appropriate equipment for packaging or bagging dry products in open-mouth or valved bags ranging from 10 to 60 kg.
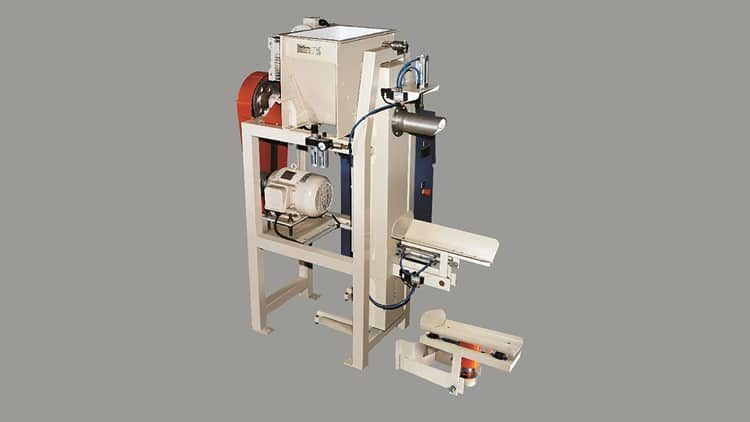
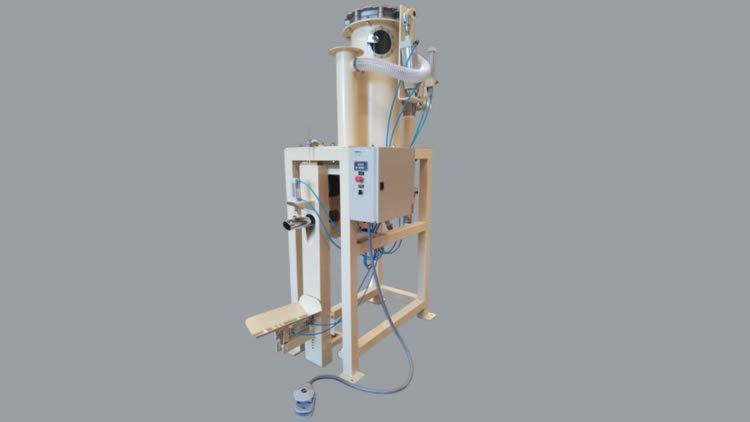
Our bagging machinery is applied in all industries, such as the milling and animal feed industries, where the production process ends with the filling of large sacks or bags.
Optional accessories for bagging systems:
We not only manufacture weighing bagging machines, but we can also offer optional elements such as:
- Bag Shapers: Provide better definition to the bag for easier palletizing.
- Ultrasonic Bag Sealer: Allows plastic film sealing even if there is dust or particles in the way.
- Product Loss or Broken Bag Recovery: Through grids and conveying systems, we can collect losses and return them to the system.
- Feeding Systems for Bagging Installation: Pneumatic or mechanical transport systems to move the product.
- Palletizing Systems: Through belts, the bags can be delivered to our automatic palletizers.
- Controlled Atmosphere Bagging: In the case of our PNBP bagger, it is possible to handle products that cannot come into contact with air. Nitrogen is typically used instead, extending the shelf life. An example of this application is powdered milk bagging.
Available bagging machine types
The choice between the different models of industrial baggers depends not only on the size of the bag to be filled and the characteristics of the product but also on the type of sack to be used: open-mouth or valve sacks.
- Screw Valved Bagger EBV 200
- Pneumatic Bagger PNBP 700
- Open-Mouth Baggers EBA
1- Screw valved bagger EBV 200
A bagging machine for valved bags that combines dosing, filling, and weighing simultaneously for bags of 10 to 60 kg. For dry products; granules or powders.
Optional:
- Bag Vibrator: For complete filling.
- Pneumatic bag holding and ejecting.
- Bag Guide to conveyor belt.
- Kit for open-mouth bag adaptation.
With pneumatic bag holding and ejecting, it operates as follows:
The operator places the bag on the spout and presses the start pedal. The bag is automatically held and begins filling.
The scale is electronic and has 2 cuts. Upon reaching the first cut, the feed speed is reduced for greater precision.
Once the final weight is reached, the bag holder releases, and the operator pushes the bag away from the spout, making it fall.
Technical information
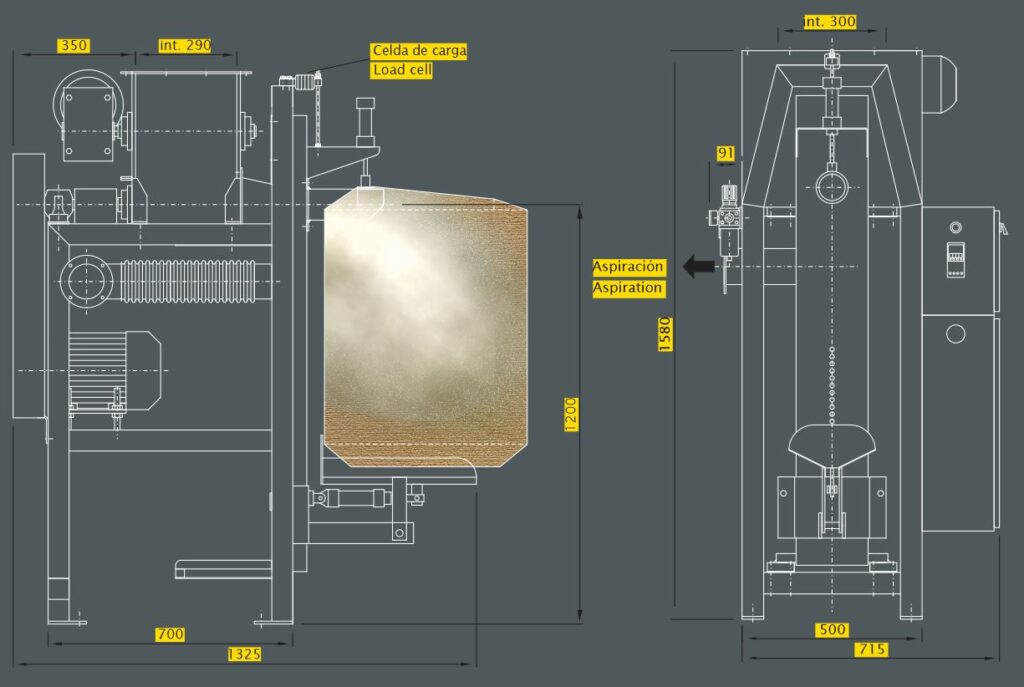
*Capacity: 150 bags of 50kg/h depending on the product, etc.
More information in the following links
2-Pneumatic bagger PNBP 700
We have launched the new version of our PNBP bagger
The 700 version features streamlined parameter programming and control, a cutting-edge electronic control system, and faster bagging speed. It perfectly adapts to the 25kg bagging required by the new legislation for Flour Mills.
We also offer the full line of equipment to supply the bagging system (sieves, filters, aspiration systems, hoppers or silos, and level controls).
The PNBP 700 bagger is the most appropriate machine for filling valve bags (it can be adapted for open-mouth bags). This bagging machine has been designed to package and weigh simultaneously fine powder or granular products, including difficult-to-handle ones: flours, starch, gypsum, lime, cement, sawdust, aluminum powder, caustic soda, refractory materials, carbon black, polycarbonate, semolina, powdered sugar, among others.
That is why our PNBP 700 sack fillers are used in industries as diverse as chemical, plastics, animal feed, mining, construction, food, and milling industries, among others.
In some cases, our bagger is the only one capable of properly bagging the product. A typical example is products sensitive to mechanical friction, which inevitably occurs in common baggers such as those that use screw filling.
This is the case with gelatin, PVC and PET powder, resins, fatty products, and wheat semolina.
It is the fastest single-spout machine on the market: in the case of wheat flour, its capacity is 380/400 bags of 50 Kg per hour.
The absence of complicated mechanisms that wear out easily allows practically eliminating maintenance services, thus saving operational costs.
If product contact with the environment through the valve of the bag could be a problem, Prillwitz recommends complementing the bagging machines with an ultrasonic bag sealing device.
Technical information
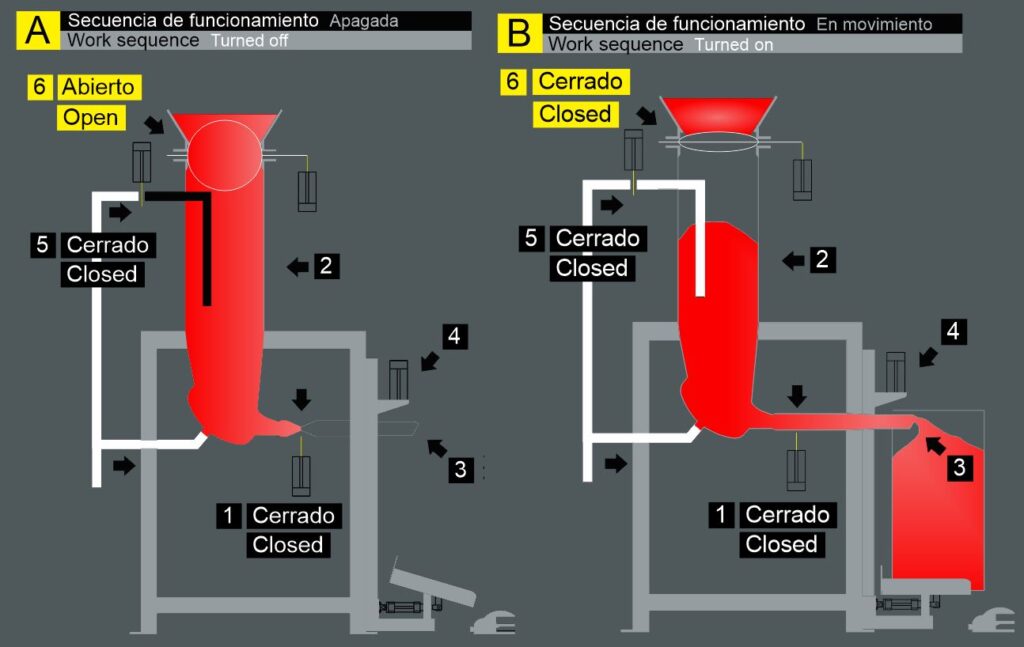
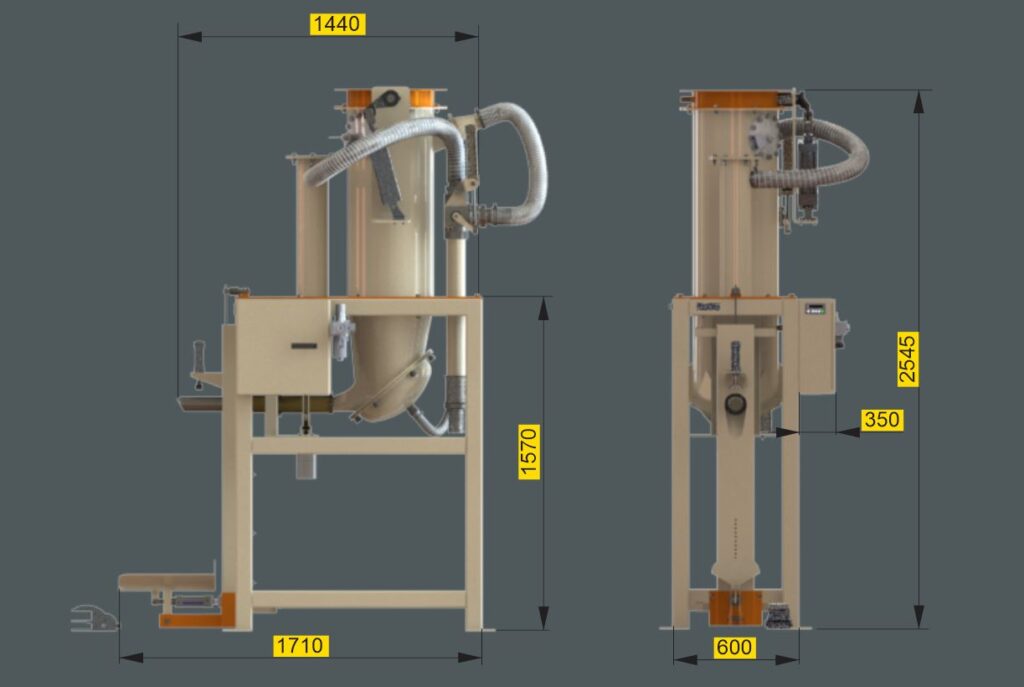
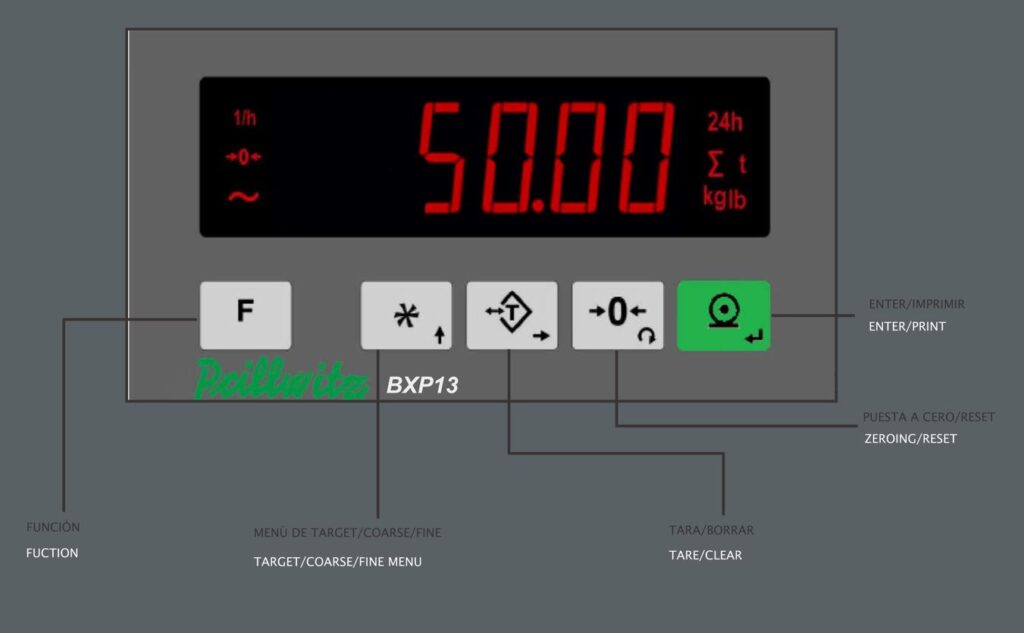
Prillwitz bagging machine PNBP 800bsxh 10-60 kg.
More information in the following links
Common raw materials for bagging:
- Wheat
- Maize
- Oats
- Coffee
- Cocoa
- Rye
- Beat
- Rice
- Girassol
- Chickpeas
- Soybeans
- Peanuts
- Peanuts
- Spices
- Balanced feed
- Pellets or feeds
- Crystalline sugar
- Impalpable sugar
- Cocoa
- Coffee
- Coriander
- Curcuma
- Gelatin
- Bone meal
- Fish flour
- Milk powder
- Dried beans
- Bread crumbs
- Batter
- Aluminum powder
- Atrazine
- Bentonite
- Borax powder
- Lime
- Caolin
- Activated carbon
- Calcium carbonate
- Cement
- Shell
- Quartz
- Titanium Dioxide
- Dolomite
- Fertilizers
- Monoammonium Phosphate
- Diammonium Phosphate
- Tricalcium Phosphate
- Mica
- Refractory Materials
- Sodium naphthalenesulfonate
- Pigments
- Soaps
- Salt
- Precipitated silica
- Caustic soda
- Magnesium sulfate
- Zinc sulfate
- Tanine
- Diatomaceous Earth
- Dyes
- Gypsum
- Lithium
- Afrecho and afrechillo
- Wheat semolina and semolina
- Semolina
- Rebasillo
- Zootechnical flour
- Maize semolina
- Semolina
- Polenta
- Wheat flour, corn flour, soy flour, etc.
- Germ
- Starch
- Hull
- Polycarbonate
- Vinyl polyvinyl chloride or PVC
- Polystyrene or PET
- Polyethylene
- Polypropylene
- Expanded polystyrene (Styrofoam)
- Sawdust
- Wood
- Cork
- Soap poder
- Pigments