With over 9 decades in building facilities for industrial grinding of dry products, our company offers a wide variety of mills that allow achieving any granulometry, from simple crushing to pulverization or micronization. Suitable for chemical, mineral, or food products.
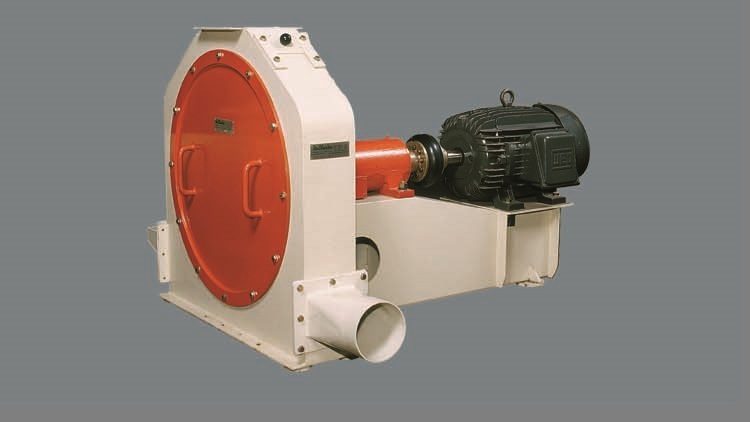
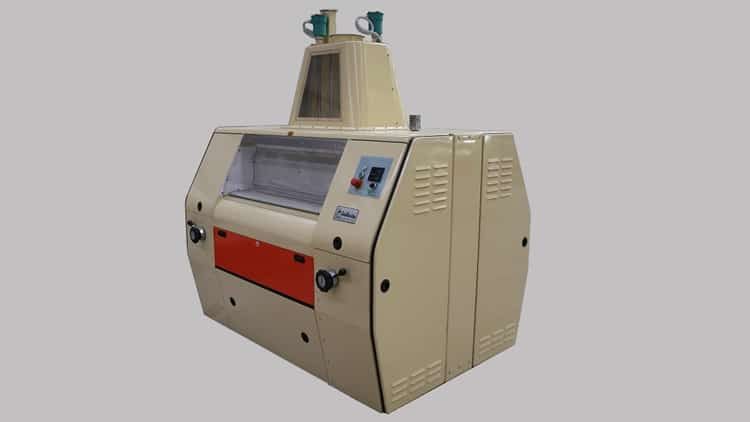
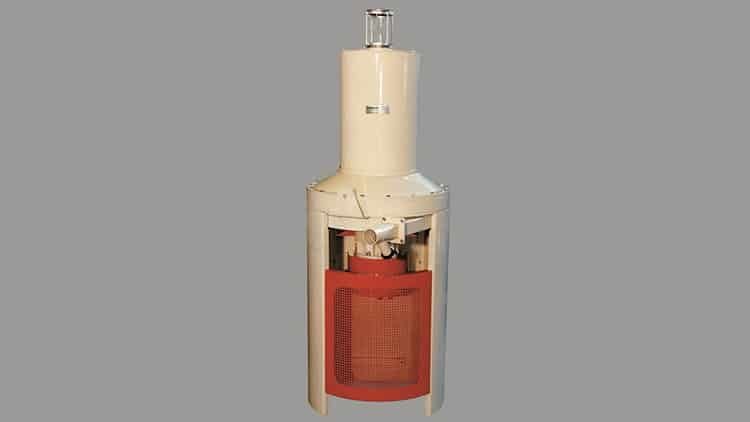
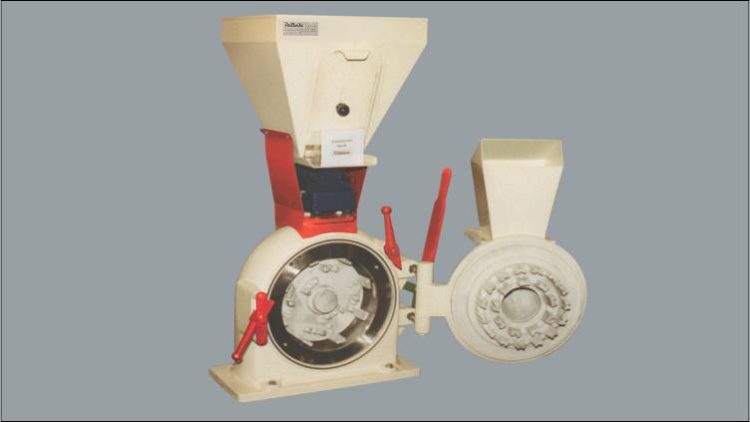
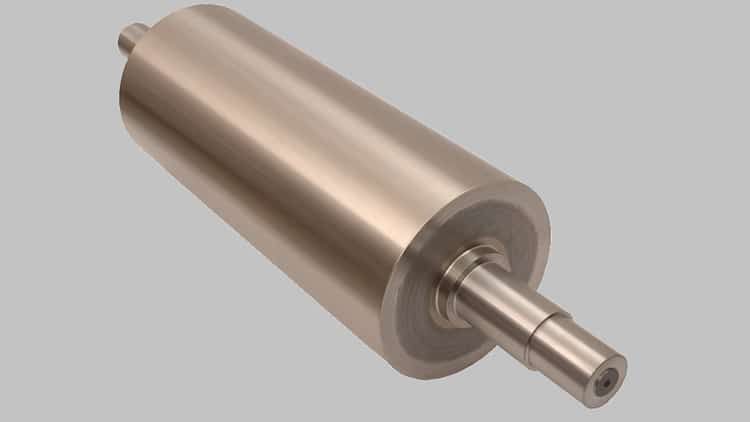
Types of mills and their most common applications.
The most important parameters to consider when determining the most suitable mill are:
- Characteristics of the product to be ground
- Required particle size distribution
- Necessary capacity
Based on this, we choose from the following mills to determine which best suits the requirement in order to establish the price:
- SIGMA hammer mill: Used when the objective of crushing or grinding is to obtain a medium or coarse particle size. Commonly used for grinding cereals.
- IMPACTOR B impact mill: Used if the aim is to achieve a fine, pulverized, or micronized particle size.
- BCH roller mill: In case grinding to intermediate particle sizes without generating a large amount of flour or very fine particles is required.
- PERPLEX disintegrator mill: For low capacities and grinding to medium or fine sizes that require integrated screening.
- DSE lump breaker: To reduce particle size or lumps to the minimum size necessary to avoid process blockages in subsequent stages.
- Laboratory mills: These allow us to analyze grinding requirements and, at the same time, test the qualities of the ground product.
Main possible forces acting on the particle to grind it
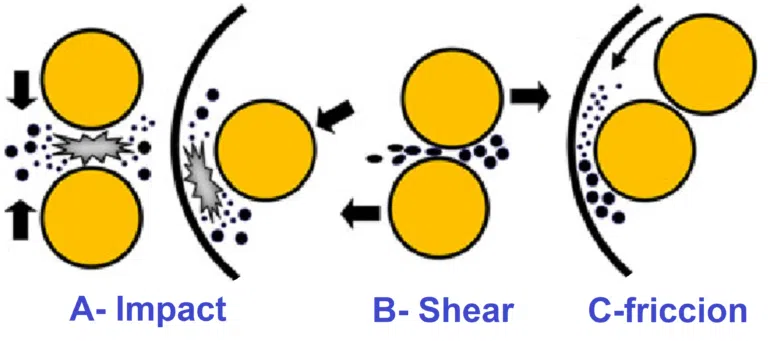
Based on the characteristics of the particle to be ground and the desired particle size distribution, the most appropriate type of force to apply is decided, and ultimately the most suitable mill. In some cases, it is recommended to combine mills of different types to achieve the objective with lower wear and energy consumption.
Example of a turnkey micronized grinding plant
Based on the characteristics of the product to be ground, as well as the required particle size distribution and capacity, our engineers determine the most suitable mill and flow diagram. Incorporating the dimensions of the available space for installation, we create the machinery and accessory assembly drawing. With all of this, along with the necessary operational logic, we design the electrical panel with PLC and screen to command the installation in an automated manner. Finally, with the assembly carried out by our highly specialized personnel, we obtain a Turnkey Grinding Plant.

01- Big Bag unloader
02- Screw conveyor
04- Cyclonic separator
05- Air filter
06- Fan
07- Rotary valve
08- Plansifter
10- Modular piping
11- Hammer mill
12- Micronizing mill
13- Level Sensor
In grinding plants, the most significant associated process is clearly Classification and Screening. However, other processes also play a role, such as:
Products that are typically ground to different particle sizes in grinding or micronization installations.
Our grinding machines are used not only in the milling of wheat and corn to obtain refined flours, but also in the milling of rice, pasta, animal feed, or other food or chemical products such as those listed below.
- Wheat
- Corn
- Oat
- Coffee
- Cocoa
- Rye
- Barley
- Rice
- Sunflower
- Chickpea
- Soybean
- Peanut
- Beans
- Spices
- Bran
- Semolina
- Zootechnical flour
- Hominy grits
- Grits
- Fodder
- Pasta
- Corn,Wheat, soya flour
- Germ
- Starch
- Husk
- Spices
- Aluminum´s powder
- Atrazine
- Bentonite
- Borax powder
- Lime
- Kaolin
- Activated coal
- Calcium carbonate
- Cement
- Quartz
- Titanium dioxide
- Dolomite
- Fertilizers
- Monoammonium phosphate
- Diammonium phosphate
- Tricalcium phosphate
- Mica
- Refractory materials
- Sodium naphthalenesulfonate
- Black carbon
- Pigments
- Soap
- Salt
- Precipitated silica
- Caustic soda
- Magnesium sulphate
- Zinc sulfate
- Tannin
- Diatomaceous earth
- Tinctures
- Gypsum
- Lithium
- Balanced feed
- Pellets
- Sugar Glass
- Icing sugar
- Cacao
- Coffee
- CorianderTurmeric
- Gelatine
- Bone´s flour
- Fish´s flour
- Milk´s powder
- Dry vegetables and leguminous
- Bread crumbs
- Sawdust
- Wood
- Cork
- Soap´s powder
- Pigments